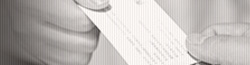
上海申弘阀门有限公司
联系人:李贤
手机:15901754341
传真:86-021-31662735
邮箱:494522509@qq.com
地址:上海市青浦区金泽工业园区
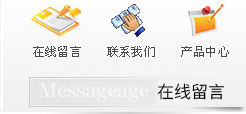
压力管道材料 |
||||||||||||||||
|
||||||||||||||||
详细介绍 | ||||||||||||||||
压力管道材料 上海申弘阀门有限公司 目录 1 金属材料基础知识 1.1金属的微观结构 1.2金属材料的基本性能 1.3温度对金属材料的影响 1.4常见元素对金属材料性能的影响 2 常用金属材料 2.1铸铁 2.2碳素钢 2.3合金钢 3 压力管道常用金属材料的基本限制条件 3.1一般限制条件 3.2 常用材料的应用限制 3.3其它方面对材料的限制 4 应用标准体系 4.1上常用的标准体系 4.2国内常用的标准体系 5 管道压力等级 6 管道器材选用 7 表面处理、防腐、涂层 8 管道施工及验收规范 1 金属材料基础知识 金属材料的基本知识仅介绍金属材料的微观结构、基本性能、常见元素对性能的影响以及金属材料的分类及牌号标识等内容。上海申弘阀门有限公司主营阀门有:ag亚博网站-ag亚博国际,电动截止阀,气动截止阀,电动蝶阀,气动蝶阀,电动球阀,气动球阀,电动闸阀,气动闸阀,电动调节阀,气动调节阀,。、、衬胶阀门、衬氟阀门。 1.1 金属的微观结构 1.1.1碳钢与铸铁 由95%以上fe+(0.05-4%)c组成的fe、c合金。 1)铁的内部结构 将铁水缓冷到其凝固点1534℃以下,铁水就开始结晶,直到全部结晶成固态铁为止,温度才又继续下降。所结晶成的固体是由许多小颗粒组成,每个小颗粒具有不规则的外形,叫晶粒。 每个晶粒内部都是由无数个原子按一定的规律排列而成。若将各个原子的中心用线条连接起来,组成一个空间格子,可用来说明原子排列的规律性,这种空间格子叫“晶格"。 常见的金属晶格形式: 面心立方晶格 体心立方晶格 ◆ fe 的晶格形式 1534℃~1390℃ 体心立方排列叫δ铁 1390℃~910℃ 面心立方排列叫γ铁 910℃以下 体心立方排列叫α铁 α铁 γ铁 δ铁 这种在固态下晶体结构随温度发生改变的现象叫“同素异构转变"。它是钢铁能够进行多种热处理而改变其性能的重要依据。 2)碳的存在形式 ◆固溶体:就是由两种或两种以上的化学元素,在固态下互相溶解构成的单一均相物质。 ◆铁素体 碳溶解在体心立方晶格fe原子之间形成的固溶体。是低碳钢在常温时的主体相。 ◆奥氏体 碳溶解在面心立方晶格fe原子之间形成的固溶体。是碳钢在高温时的组织。 ◆渗碳体:铁碳合金中的碳不能全部溶入铁素体、奥氏体中时, “剩余"的碳与铁形成的铁碳化合物(fe3c)的晶体组织。 ◆石 墨:铸铁中的c >2.06% ,奥氏体zui大溶碳量2.06%,剩余的c以石墨形式存在。 1.1.2铁碳合金相图(相图略) 铁碳合金相图 是表示不同成分的铁碳合金在不同温度下所具有的状态或组织的关系图。 相图的作用 通过铁碳合金相图能掌握钢的组织随成分和温度变化的规律,以便能够正确制定热处理和热加工的工艺,是改变其组织,获得所需要的性能的依据。 相图中有: 两个组元: 铁(fe) 性能表现为强度和硬度较低,塑性和韧性较好 渗碳体(fe3c) 性能表现为硬而脆 四个基本相:液相(l)、铁素体(а)、奥氏体(γ)和渗碳体(fe3c) 两个次生相:珠光体(铁素体+渗碳体的两相机械混合物)具有良好的强度和硬度又具有良好的塑性和韧性,属常温稳定组织 莱氏体(奥氏体+渗碳体的两相机械混合物) 在平衡状态下: c=0.8% 珠光体 共析钢 c<0.8% 铁素体+珠光体 亚共析钢(gs亚共析钢线) c>0.8% 渗碳体+珠光体 过共析钢(es过共析钢) gs线:c<0.8%的铁碳合金加热时铁素体向奥氏体转变的终了温度线(ac3),或者冷却时奥氏体向铁素体转变的开始温度线(ar3)。 es线: 0.8% psk线:铁碳合金加热时珠光体向奥氏体转变的温度线(ac1),或者冷却时奥氏体向珠光体转变的温度线(ar1)。 1.1.3碳钢的热处理 ● 热处理:就是利用钢在固态范围内的加热、保温和冷却以改变其组织,获得所要求的性能。按照热处理的操作及其过程所发生的组织变化的不同,将热处理分为淬火、回火、退火及化学热处理。 淬火:是将钢加热至超过临界温度以上,保温一定时间后,以快速冷却,使其得不到稳定的组织。 目的:是为了获得马氏体以提高工件的硬度和耐磨度。 回火:是将淬火后的钢重新进行不超过临界温度(gs线)时加热,使之得到较为稳定的组织。根据对零件机械性能的具体要求回火的加热温度分为低、中、高温三种。 目的:消除淬火后工件的内应力,并降低材料的脆性。钢件在淬火后,几乎总是跟着回火。 退火:退火处理时用来消除钢材在焊接、铸造或锻造后下来的粗晶组织和内应力,降低硬度,增加塑性和韧性,消除偏析。 完全退火—将钢加热到gs线以上20~30℃,经保温后随炉缓冷或埋在保温灰中缓冷。 低温退火—加热至小于临界点psk的温度而后缓慢冷却。 目的是消除工件在焊接过程中所形成的内应力,以防脆裂。 正火:是退火的一种变态,它与退火不同之处是在静止空气中冷却。 1.1.4 常用压力管道材料使用的热处理状态 1.2金属材料的基本性能 金属材料的基本性能一般包括: 机械性能、耐腐蚀性能、物理性能、制造工艺性能和经济性。 l.2.1机械性能(5.13/p168) 材料的机械性能是指在外力的作用下,材料抵抗破裂和过度变形的能力。 它包括材料的强度指标、弹性指标、塑性指标、韧性指标、疲劳强度、断裂韧度和硬度等。 1.2.2.耐腐蚀性能(化学性能) 腐蚀不仅会造成金属的损失,更重要的是会导致金属的破坏,从而威胁到压力管道的安全。事实已证明,许多压力管道的破坏都与材料的腐蚀有关。 ◆ 材料的选择应避免应力腐蚀的发生,因为它会带来压力管道在不可预知的情况下突然断裂,从而导致重大事故的发生; ◆ 选用的材料应有足够的抗介质均匀腐蚀的能力,以便材料不致于在短时间内因腐蚀造成的管道壁厚急剧减薄而失效。等等。 1.2.3物理性能 材料的物理性能主要是指: 密度ρ(kg/m3)、导热系数、比热、熔点tm(℃)、线膨胀系数、弹性模量e、比重 1.2.4.制造工艺性能 材料的制造工艺性能也是影响材料选择的一个重要因素,主要有: 1) 切削加工性能; 2)可铸性;3)可锻性; 4)可焊性; 5)热处理性能; 1.2.5材料的经济性 材料的选择不能脱离经济性这个杠杆作用,这就是工程材料研究与一般材料研究区别的显著标志。选材的原则: 1) 设计选材既要可靠,又要经济,能用低等级材料时就不要选用高等级材料。 2) 对材料的制造要求也应适当,要结合使用条件来规定各项检查试验要求。 3) 对于每一种金属材料来说,以上各类性能不可能都是的,选用材料时,只能扬长避短,物尽其用。 1.3 温度对金属材料性能的影晌 1.3.1金属材料在高温下的性能变化 1)材料的蠕变及应力松弛 材料的蠕变: 当材料的使用温度超过其熔点的(0.25~0.35)倍时,金属性能已处于不稳定状态,此时若在外力的作用下,会出现这样一种现象:虽然材料的应力不再增加,但其变形却随着时间的增加而继续增大,而且出现了不可恢复的塑性变形。 ◆一般情况下,对碳钢,考虑蠕变发生的起始温度为300~350℃,对铬钼合金钢则为400~450℃。 应力松弛:与蠕变现象相反,当材料受高温和外力的持续作用时可能会出现:材料的总应变量不变,使其中部分弹性变形转化成了塑性变形,从而导致弹性应力降低,即意味着金属材料被"放松"了。 2)材料的球化和石墨化 材料的球化:在高温作用下,碳钢中的渗碳体由于获得能量而将发生迁移和聚集,形成晶粒粗大的渗碳体并夹在铁素体内,尤其是对于珠光体碳钢,其渗碳体会由片状逐渐转变成球状。这种现象称为材料的球化。 球化的结果:使得材料的抗蠕变能力和持久强度下降,而塑性增加。 ◆ 一般情况下,碳钢长期处于450℃以上温度环境时,就有明显的球化现象。 材料的石墨化:对于碳钢和一些低合金钢,在高温作用下,其组织中会出现这样一种现象:其过饱和的碳原子发生迁移和聚集,并转化为石墨(石墨为游离的碳原子)。由于石墨强度极低,并以片状存在于珠光体内,将使材料的强度大大降低,而脆性增加。这种现象称为材料的石墨化。 ◆一般情况下,碳钢长期处于425℃以上温度环境时,就有石墨化发生,而在475℃以上时则明显出现。sh3059标准规定,碳钢的zui高使用温度为425℃,而gb150规范则规定其zui高使用温度为450℃。 3)材料的高温氧化 金属的氧化 金属材料处于高温和氧化性介质(如空气)的环境中时,将会被氧化。氧化产物为疏松的非金属物质,容易脱落,故有时也称其金属的氧化为脱皮。 1.3.2金属材料在低温下的性能变化 在低温情况下,材料因其原子周围的自由电子活动能力和“粘结力"减弱而使金属呈现脆性。一般情况下,对于每种材料,都有这样一个临界温度,当环境温度低于该临界温度时,材料的冲击韧性会急剧降低。通常将这一临界温度称为材料的脆性转变温度。为了衡量材料在低温下的韧性,常用低温冲击韧性<冲击功>来衡量. 1.4 常见元素对金属材料性能的影晌 黑色金属材料的基本元素是铁(fe),所以对材料性能的影响主要是指铁以外的其它元素。 1.4.1常用碳素钢中各元素对其性能的影响 碳素钢中,其主要影响元素是碳(c)。除此之外,尚有硅(si)、硫(s)、氧(0)、磷(p)、砷(b)、锑(sb)等杂质元素 a 碳(c)在碳素钢中的作用 b硅(s)在碳素钢中的作用 c硫(s)、氧(0)在碳素钢中的作用 d磷(p)、砷(as)、锑(sb)在碳素钢中的作用 1.4.2.常用低合金钢中各元素对其性能的影响 管道中除螺栓材料外,常用的低合金钢为含碳量小于0.20%的碳锰钢、硅钢、铬钼钢、铬钼钒钢和铬钼钒铝钢,而螺栓材料则常用含碳量为0.25%~0.45%的铬钢和铬钼钢。 主要影响元素:碳(c)、锰(mn)、铬(cr)、mo、v、si、al 杂 质 元 素:s、o、p、as、sb、 a碳(c)在低合金钢中的作用同碳素钢部分。 b锰(mn)在低合金钢中的作用 c铬(cr)在低合金钢中的作用 d钼(mo)在低合金钢中的作用 e 钒(v)在低合金钢中的作用 f 硅(st)在低合金钢中的作用 g 铝(al)在低合金钢中的作用 h硫(s)、氧(0)、磷(p)、砷(as)、锑(sb)等杂质元素同在碳素钢中的作用。 1.4.3常用高合金钢中各元素对其性能的影响 压力管道中常用的高合金钢为含碳量小于0.10%的铬钼、铬镍、铬镍钼耐热钢和不锈钢。 高合金钢中,其主要影响元素:碳(c)、铬(cr)、钼(mo)、镍(ni)、钛(ti)、硅(si)等; 杂质元素:硫(s)、磷(p)、砷(as)、锑(sb)等。 a碳(c)在高合金钢中的作用 b钼在高合金钢中的作用 与在低合金钢中的作用相似。 c镍(ni)在高合金钢中的作用 d 钛(ti)在高合金钢中的作用 e硅(s)在高合金钢中的作用 2常用金属材料 2.1 铸铁 2.1.1灰口铸铁 2.1.2可锻铸铁 2.1.3球墨铸铁 2.2 碳素钢 2.2.1.碳素钢的分类 2.2.2普通碳素钢 2.2.3碳素钢 2.2.4碳素钢 2.3 合金钢 2.3.1合金钢分类 2.3.2常用合金钢 2.4 常用金属材料技术条件标准 2常用金属材料 介绍压力管道中常用的金属材料的分类、特点、用途和表示方法 金属材料:黑色金属: 通常指铁和铁的合金 有色金属: 指铁及铁合金以外的金属及其合金。 黑色金属根据它的元素组成和性能特点分为三大类,即铸铁、碳素钢及合金钢。 2.1铸铁 铸 铁:含碳量大于2.06%的铁碳合金 。 ◆真正有工业应用价值的铸铁其含碳量一般为2.5%~6.67%。 ◆ 铸铁的主要成分除铁之外,碳和硅的含量也比较高。由于铸铁中的含碳量较高,使得其中的大部分碳元素已不再以fe3c化合物存在,而是以游离的石墨存在。 性能特点:是可焊性、塑性、韧性和强度均比较差,一般不能锻,但它却具有优良的铸造性、减摩性、切削加工性能,价格便宜。 用 途:常用作泵机座、低压阀体等材料;地下低压管网的管子和管件。 根据铸铁中石墨的形状不同将铸铁分为灰口铸铁、可锻铸铁和球墨铸铁。 2.1.1灰口铸铁:石墨以片状形式存在于组织中的铸铁称之为灰口铸铁。 ◆灰口铸铁浇铸后缓冷得到的组织为铁素体和游离石墨共存,断口呈灰色,灰口铸铁也因此而得名。灰口铸铁的各项机械性能均较差,工程上很少使用。 2.1.2可锻铸铁:经过长时间石墨化退火,使石墨以团絮状存在于铸铁组织中,此类铸铁称为可锻铸铁。 性能特点:强度、塑性、韧性均优于灰口铸铁,其延伸率可达12%;但可锻铸铁制造工艺复杂,价格比较高。 ◆由于可锻铸铁具有一定的塑性,故"可锻"的名称也由此而出,其实它仍为不可锻。 用 途:可锻铸铁在工程上常用作阀门手轮以及低压阀门阀体等。 根据断面颜色或组织的不同,可锻铸铁又分为黑心可锻铸铁、白心可锻铸铁和珠光体可锻铸铁三种。常用的是黑心可锻铸铁。 2.1.3球墨铸铁:是通过在浇注前向铁水中加入一定量的球化剂进行球化处理,并加入少量的孕育剂以促进石墨化,在浇注后直接获得具有球状石墨结晶的铸铁。 性能特点:球墨铸铁的各项性能指标均优于可锻铸铁,比可锻铸铁价格便宜。 用 途:可代替可锻铸铁用在较苛刻条件下。用途更广泛。 铸铁命名:根据gb9439的规定铸铁的牌号表示方法:
2.2碳素钢 碳素钢:含碳量小于等于2.06%的铁碳合金称为碳素钢。 2.2.1.碳素钢的分类 2.2.2普通碳素钢 ◆普通碳素钢与碳素钢相比,由于它的有害杂质元素s、p含量相对较高,综合机械性能和耐蚀性较差,故不宜用在较重要的场合,但普通碳素钢价格便宜,故工程上常用于各种钢构架、支吊架等,而流体输送管道上使用时常给与一定的限制。 ◆普通碳素钢根据冶炼过程的脱氧程度分为沸腾钢、镇静钢和半镇静钢三种。 沸腾钢:在浇铸前不用硅和铝脱氧, 钢液中含氧量多,浇注及凝固时会产生大量co气泡,在钢锭模内产生沸腾现象,这类钢叫沸腾钢。 沸腾钢冷凝后没有集中缩孔,因而成材率高,成本低,表面质量及深冲性能好。但因含氧量高,成分偏析大,内部杂质多,抗腐蚀性和机械性能差,.且容易发生时效硬化和钢板的分层,故不宜作重要用途。 镇静钢:而脱氧较完全,浇铸时钢水在钢锭模内不产生co气体,这类钢叫镇静钢。 成材率低,成本高。但镇静钢中气体含量低,时效倾向小,钢镜中气泡、疏松较少,质量较好。 半镇静钢:进行中等程度脱氧,介于沸腾钢和镇静钢之间的钢叫。 普通碳素钢的表示方法和代号按gb700标准 ◆压力管道中常用的普通碳素结构钢牌号为q23(f、b)、q235b(f、b)、q235c、q235d四种,这些牌号的质量要求是顺次提高的。材料标准为gb700。 2.2.3碳素钢 ◆碳素钢中的有害杂质元素s、p比普通碳素钢低,不仅如此,二者的冶炼方法也多有不同,普通碳素钢多用成本zui低转炉冶炼,而碳钢则采用平炉或纯氧顶吹转炉冶炼,脱氧较好,杂质含量较低,故其综合机械性能、耐蚀性等均优于普通碳素钢。碳素钢与碳素钢相比,价格不高,且是工程上应用zui广泛的碳素钢。 ◆碳素钢的表示方法和代号按gb221标准: ◆ gb/t699给出了碳素钢的化学成分和机械性能要求。 该标准共列出了08f、10f、15f、08、10、20、25、……70mn等31种材料牌号; 压力管道中常用的牌号为08、10、20三种。 2.2.4碳素钢 碳素钢各方面性能略优于碳素钢,但价格较高,工程上用的并不多。一般情况下,如果采用碳素钢不能满足使用条件要求时,将考虑选用相应的合金钢而不用碳素钢。碳素钢在碳素钢的牌号后加a 2.3合金钢 合金钢:为了提高钢的机械性能、工艺性能或物理化学性能,通常有意识地向钢中加入一些合金元素,由此得到的钢就叫合金钢。 2.3.1合金钢分类 表2-1合金钢分类(用途) *层 第二层分类 第三层分类 特点及用途 合金钢 合金结构钢 低合金钢 1.低碳型合金钢,合金元素总量一般≯3%; 2.强度明显高于碳素钢,有较好的塑性和韧性,可焊性尚可; 3.用于中高温、抗氢、抗高温硫腐蚀等。 调质钢 1.中碳型合金钢,合金元素含量较低; 2.强度较高; 3.用于高温螺栓、螺母材料等。 弹簧钢 1含碳量比调质钢高; 2经调质处理,强度较高 抗疲劳强度较高; 3用于弹簧材料。 滚动轴承钢 1高碳型合金钢,合金含量较高; 2具有高而均匀的硬度和耐磨性; 3用于滚动轴承。 合金工具钢 量具钢 1高碳型合金钢,合金元素含量较低; 2具有高的硬度和耐磨性,机加工性能好,稳定性好; 3用于量具材料。 特殊性能钢 不锈钢 1低碳高合金钢; 2抗腐蚀性好; 3用于抗腐蚀、部分可做耐热材料。 耐热钢 1低碳高合金钢; 2耐热性能好; 3用于耐热材料、部分可做抗腐蚀材料。 低温钢 1低碳合金钢,根据耐低温程度合金元素有高有低; 2抗低温性好; 3用于低温材料(钢为镍钢)。 合金元素因溶于铁素体中起固溶强化作用,从而提高了材料的硬度和强度,但同时却使其韧性和塑性相对降低。 材料在低温下强度一般略有提高,但塑性和韧性则下降很多,通过添加一些合金元素可提高材料在低温下的塑性和韧性。 奥氏体不锈钢由于含有较多的合金元素又具有单一的奥氏体组织,故它具有较好的抗氧化腐蚀性能和高温使用性能。工程上,奥氏体不锈钢常用于多种腐蚀工况和高温工况。 合金钢的优点 合金钢与碳素钢相比,它具有较高的强度,较好的耐热性,较好的耐低温性能,较好的耐腐蚀性能等优点,甚至有些生产环境采用碳素钢是满足不了要求的。故合金钢是压力管道中常用的也是很重要的材料。 2.3.2常用合金钢 压力管道中常用的合金钢有低合金钢、调质钢、不锈钢、耐热钢和低温钢。其它钢种有时也会偶尔碰到在此不再作进一步的介绍。 a.低合金钢 低碳型合金钢,合金元素总量一般≯3%;强度明显高于碳素钢,有较好的塑性和韧性,可焊性尚可;低合金钢有碳锰系、碳锰钒系、铬钼系、铬钼钒系 ◆碳锰系和碳锰钒系 gb/t1591给出了化学成分和机械性能要求; l 材料牌号为q29(b)、q34~e、q390a~e、q420a~e、q460c~e; l 用于常温及以上温度时,可用a、b或c级;用于-20~-40℃ 时,可用c或d级 l 表示方法及代号同普通碳素钢 ◆铬钼系和铬钼钒系 gb/t3077给出了化学成分和机械性能要求; l 材料牌号主要为12crmo、15crmo、12cr1mov; l 它们常用作抗氢腐蚀、抗高温硫或硫化氢腐蚀和耐热(次高温)等材料 例如,12crmo和15crmo常用于550℃以下的高温工况,或用于320℃以下的临氢工况;12crlmov常用于575℃以下的高温高压蒸汽介质。 l 表示方法及代号 b.调质合金钢 l 中碳型合金钢,合金元素总量一般≯3%; l 它的含碳量较高,强度高,可焊性差; l gb/t3077给出了化学成分和机械性能要求; l 材料牌号为40cr、45cr、30crmo、30crmoa、35crmo、35crmoa、25crmova 等 l 用于螺栓、螺母材料 l 表示方法及代号同低合金钢中的铬钼系和铬钼钒系 c.不锈钢 ◆不锈钢特点 l 合金元素含量比较高,均超过10%,有的高达50%甚至更多; l 它含有大量的合金元素,故其耐热、耐蚀等性能大大优于碳素钢和低合金钢,但随之而来的是其价格也远远高于碳素钢和低合金钢。 ◆分类(按常温的组织不同) 奥氏体型 奥氏体-铁素体双相型 铁素体型 因钢管表面状态的影响所形成的腐蚀电池。如制管缺陷、夹杂等,当这些部位与土壤接触时,由于电极电位差而构成腐蚀电池。② 宏观腐蚀电池:因土壤介质差异引起的腐蚀电池。如:土壤的含盐量、含氧量、透气性等,它们的浓度对管材/土壤的电极电位值影响很大。 (2)杂散电流腐蚀。这是散流于大地中电流对管道所产生的腐蚀,又名干扰腐蚀。是一种外界因素引起的电化学腐蚀,由外部电流极性和大小来决定,其腐蚀比一般土壤腐蚀激烈得多。对于绝缘不良的管道,杂散电流可能在绝缘破损的某一点流入管道,然后沿管道流动,在另*缘破损点流出,返回杂散电流源,从而引起腐蚀。这些杂散电流源主要由于电气化铁道、电解工厂直流电源、阴极保护设施、交直流高压输电系统接地极所产生。 (3)细菌腐蚀(微生物腐蚀)。细菌在特定的条件下参与金属的腐蚀过程。埋藏在土壤中的钢铁管道表面,由于腐蚀,在阴极上有氢产生,如果附在金属表面不成为气体逸出,则它的存在就会造成阴极极化而减缓腐蚀进程,甚至停止进行腐蚀。如果有硫酸盐还原菌活动,恰好利用金属表面的氢把so42- 还原,促进了阴极反应,使腐蚀速度加快。特别的,有一些细菌是依靠管道防腐涂层的石油沥青作为养料,将沥青“吃掉",从而造成防腐层被破坏而丧失防腐功能。 (4)大气腐蚀(微生物腐蚀)。管道表面金属置于大气环境中时,其表面通常会形成一层极薄的不易看见的湿气膜(水膜),当这层水膜达到20-30个分子厚度时,它就变成电化学腐蚀所需要的电解液膜,大气环境下形成的水膜往往含有水溶性的盐类及溶入的腐蚀性气体(如二氧化碳),导致管道表面发生电化学腐蚀。 影响埋地输油管道腐蚀速度的因素是多方面的,主要决定于土壤的性质。而表征土壤性质指标的各种参数均会对管道金属的腐蚀产生影响,如土壤 ph 值、氧化还原电位、土壤电阻率、含盐种类和数量、含水率、孔隙度,有机质含量、温度、细菌、杂散电流等。而其中 ph 值、土壤电阻率、含盐种类和数量是主要因素,分析埋地输油管道腐蚀剩余寿命必须以此为依据。 1.2 输油、输气钢管防腐技术 1.2.1输油、输气钢管防腐要求 埋地输油、输气钢管防腐形式通常有管道内防腐、管道外防腐、管道阴极保护、地上管道防腐。对埋地管道外防腐蚀涂层的要求:具有良好的抗土壤、水、霉菌的腐蚀和施工性能,有良好的电绝缘性,阴极保护联合使用时防腐涂层应具有一定的耐阴极剥离强度的能力,有足够的机械强度,以确保涂层在搬运和土壤压力作用下无损伤。 1.2.2输油、输气钢管防腐技术简介 埋地钢管外防腐涂装技术有石油沥青防腐层,环氧煤沥青防腐涂层、煤焦油瓷漆防腐涂层、聚乙烯粘胶带、熔结环氧粉末防腐涂层、二层pe防腐涂层,三层pe防腐涂层、聚氨酯硬质泡沫塑料防腐保温复合结构。后三种方法是通常使用的方法。 1.2.3补口热缩带简介 补口热缩带系列产品是为埋地及架空钢质管道焊口的防腐和保温管道的保温补口而设计的,也可用于管道法兰连接部位、锁箍部位的密封防腐。它是由辐射交联聚烯烃基材和特种密封热熔胶复合而成,特种密封热熔胶与聚烯烃基材、钢管表面及固体环氧涂层可形成良好的粘接。热收缩带在加热安装时,基材在径向收缩的同时,内部复合胶层熔化,紧紧地包覆在补口处,与基材一起在管道外形成了一个牢固的防腐体,具有优异的耐磨损、耐腐蚀、抗冲击及良好的抗紫外线和光老化性能。此外除了补口热缩带主体,还配有胶条和固定片,且补口热缩带便于规模化生产,施工也方便很多。 2、防腐补口的施工工艺和方法 2.1沥青热浇涂补口 原料可以为石油沥青(也可以是煤焦油瓷漆)加缠玻璃布,薄涂多层结构,厚度等同于管道防腐层,施工方法为现场热浇涂,适用于相同材料的管道防腐层。中洛线“管中管"施工时部分补口曾采用此方法,效果尚可,其优点是原材料广泛、价格低廉;缺点是现场热浇涂劳动条件差,质量难以保证,施工时对环境有污染等。在国内应用较广泛,在国外已处于被淘汰之列。 2.2热烤沥青缠带补口 原料为浸涂过焦油瓷漆或石油沥青的玻璃纤维毡缠绕带,现场边加热边缠绕形成多层结构,厚度等同于管道防腐,适用于相同材料的管体防腐补口。优点为原材料广泛,与管体为同种材料时熔结较好;缺点是操作步骤较复杂,人为因素影响大,如烘烤温度的掌握、烘烤的均匀性等,都对粘结力有决定性的影响。在国外有一定数量的使用,国内尚未大量应用。 2.3聚乙烯胶粘带补口 结构为先涂刷与胶粘带配套的底漆,然后缠绕聚乙烯胶粘带作为防腐层,外保护层采用聚氯乙烯或聚乙烯外缠带,其厚度和层数根据防腐层等级确定。其优点是施工速度快,不需加热,操作简单;缺点为粘结力较差,防水性能低,受施工环境影响较大,强度低。该方法不仅可应用于聚乙烯胶粘带防腐的补口,还可用于聚乙烯包覆、融结环氧粉末、三层防腐层的补口。国内外有一定规模的应用。 2.4环氧煤沥青补口 原料为环氧煤沥青漆加玻璃布,薄涂多层结构,现场冷涂。适用于管体防腐为同种材料的管段。优点是现场操作简便,不需加热;缺点为涂层固化时间长,不适合野外作业,环境温度10〔c以下就难以施工。国内在厂区、市区的管道上应用较多,野外长输管道很少使用。 2.5环氧粉末补口 原料为环氧粉末,施工方法和管体预制厂内涂敷相同,即现场喷砂除锈(sa2.5级)、静电加热喷涂。适用于管体防腐为环氧粉末的补口。优点是与管体防腐是同种材料时熔结好,与钢管粘结力强;缺点为对现场机具要求高,难度大,费用高。国内在河流定向钻穿越段和小规模管道中采用过,国外应用较多。另有一种使用液态环氧涂料现场涂刷补口的方法,施工操作简单,但涂层的技术性能比热喷涂环氧粉末降低很多,只宜用在因地形等原因不能进行热喷涂补口的场合。 2.6聚乙烯电热熔套补口 原料为与管体防腐相同的聚乙烯片材电阻丝,施工方法是电热熔套用机具卡紧后,通上电流加热管体与补口材料搭接处的电阻丝,使搭接部分在熔融状态下粘合,达到密封防水、外防护层的作用。适用于聚乙烯包覆和“管中管"防腐保温层的补口。优点是与管体防腐是同种材料时熔融好,施工质量便于现场(充气)检验;缺点为现场施工需相应的机具,对操作人员经验有较高要求。国内在聚乙烯包覆和“管中管"结构上均有一定规模的采用,国外在“管中管"结构应用上居多。 2.7幅射交联聚乙烯热收缩套(片)补口 原料为经过幅射交联的聚乙烯片材,内敷热熔性胶粘剂。施工时将其套(包覆)在补口处,均匀加热产生径向收缩,内层胶熔化,使收缩套(片)紧密地与管体防腐层和补口钢管表面粘接在一起,达到密封防腐作用。优点是密封性强、粘结力好、施工较方便、适用性广、无环境污染等;缺点为施工受雨雪、风沙天气影响大,对操作工的责任感、熟练程度有较高要求。该方法适应各种管体防腐材料的补口。目前在国外应用zui广泛,国内在“管中管"结构上应用较广。 2.8复合结构补口 主要应用于近年来国外兴起的三层复合结构(环氧粉末一胶粘剂一聚乙烯外包覆层)上。施工时先将钢管表面除锈至sa2.5级,加热后喷涂环氧粉末(或涂刷液态环氧涂料),在其胶化与固化过程中包覆幅射交联聚乙烯热收缩套(片)。优点是与管体防腐结构相近时的防腐、防护密封性能可靠;缺点为对施工机具要求高,工艺较复杂、费用高。国外在三层结构防腐层补口中的应用占有相当高的比例。另外还有自粘接油毡、玻璃钢补口等方法,它们的适用范围较小,应用很少。 3、西二线线路主要防腐补口施工工艺 西二线线路管道主要采用复合结构补口,分干膜施工和湿膜施工两种,采用干膜施工的品牌有canusa,采用湿膜施工的品牌有西普、长圆和双流热收缩带。 3.1干膜施工和湿膜施工 干膜(dry film)在涂状中是相对湿膜(wet film)而言的。底漆在未完全干燥前称为湿膜,完全干燥后贴附在被涂物质表面的油漆就成干膜。干膜实际上是真正涂在被涂表面干燥固化的成膜,其他物质如溶剂和稀释剂则挥发在大气中了。 干膜施工在进行下道工序前底漆已成膜,易于检查其成膜完整性、厚度等,但是干膜安装是否会影响热缩带的粘接性能,目前业界尚未形成统一认识。湿膜施工无法检查成膜厚度和缺陷,且在施工过程中容易导致底漆损伤和脱落。 2003年以后,几乎所有的管线补口规范都明确规定了环氧底漆必须采用干膜施工,同时对环氧底漆的检查提出要求。 3.2防腐补口流程 图1防腐补口流程图 3.3西二线补口材料主要技术要求 表1热收缩带的厚度 单位:mm 适用管径 基材厚度 胶层 ≤400 ≥1.2 ≥1.0 >400 ≥1.5 表2热收缩带基层的性能指标 序号 项目 性能指标 试验方法 1 拉伸强度(mpa) ≥17 gb/t 1040.2 2 断裂伸长率(%) ≥400 gb/t 1040.2 3 维卡软化点(℃) ≥90 gb/t 1633 4 脆化温度(℃) ≤-65 gb/t 5470 5 电气强度(mv/m) ≥25 gb/t 1408.1 6 体积电阻率(ω·m) ≥1×1013 gb/t 1410 7 耐环境应力开裂(f50)h ≥1000 gb/t 1842 8 耐化学介质腐蚀 (浸泡7d)% 10%hcl ≥85 10%naoh ≥85 10%nacl ≥85 9 耐热老化 (150℃,21d) 拉伸强度(mpa) ≥14 gb/t 1040.2 断裂伸长率(%) ≥300 gb/t 1040.2 10 热冲击(225℃,4d) 无裂纹、无流淌、无垂滴 表3热收缩带胶层的性能指标 序号 项目 性能指标 试验方法 1 胶软化点(环球法)℃ ≥110 gb/t 4507 2 搭接剪切强度(23℃)mpa ≥1.0 gb/t 7124 3 搭接剪切强度(70℃±2℃) mpa ≥0.05 gb/t 7124 4 脆化温度℃ ≤-15 5 剥离强度n/cm 收缩带/钢(23℃) (70℃) 收缩带/环氧底漆钢(23℃) (70℃) 收缩带/聚乙烯层(23℃) (70℃) 内聚破坏 ≥70 ≥10 ≥70 ≥10 ≥70 ≥10 gb/t 2792 拉伸速率为10mm/min。 表4热收缩带底漆的性能指标 序号 项目 性能指标 试验方法 1 剪切强度(mpa) ≥5.0 gb/t 7124 2 阴极剥离(65℃,48h) mm ≤10 拉伸速率为2mm/min。 表5热收缩带安装系统的性能指标 序号 项目 性能指标 试验方法 1 抗冲击强度(j) ≥15 gb/t 7124 2 阴极剥离(70℃,30d) mm ≤25 3 耐热水浸泡(70℃,120d) 无鼓泡、无剥离、膜下无水 4 剥离强度n/cm 收缩带/环氧底漆钢(23℃) (70℃±5℃) 收缩带/聚乙烯层(23℃) (70℃±5℃) 内聚破坏 ≥70 ≥10 ≥70 ≥10 维卡软化点:工程塑料、通用塑料等聚合物的试样于液体传热介质中,在一定的载荷、一定的等速升温条件下,被1m㎡的压针压入1mm深度时的温度。热缩带胶黏剂的维卡软化点,在50℃运行条件下,其维卡软化点为90℃。维卡软化点对于确保在运行温度条件下聚乙烯层的温度强度具有重要意义。 3.4国内外热缩带差异 一、补口热缩带厚度的差异 迄今为止,除了中国外,世界上所有热缩带的厚度结构采用的是基材厚度为1mm,胶粘剂厚度为1.5mm的标准结构,这个厚度结构不仅仅在各个项目中得到应用,而且在用的设计手册和标准化手册中予以明确的规定。 目前国内的技术标准采用的是基材大于1.5mm,胶粘剂大于1.0mm的结构,这种结构正好与标准相反。 这种差异导致在安装中出现如下问题: a、基材厚度变厚之后热缩带胶粘剂烘烤融化就会变得困难,也无法控制和掌握,特别是在冬季施工的项目。 b、基材厚度变厚之后导致搭接处空隙变大,容易出现空鼓现象,国内部分厂家为了弥补这一缺陷,采用加热熔胶条的方法补救,但是效果不好。 导致这一情况产生的主要原因:1、国内目前的设计规范还未与接轨。2、基材聚乙烯材料的价格便宜,成本容易控制。 二、补口热缩带材料的差异 迄今为止,国内补口材料全部采用的是低密度聚乙烯材料(0.91-0.92g/cm3),这种材料的强度低、易破损。根据目前的技术标准,特别是1219mm直径的大口径、高温运行的管线,全部明确规定必须采用高密度聚乙烯材料。为了确保管线的补口防腐蚀质量,上已经开始放弃使用聚乙烯材料(包括高密度聚乙烯材料),更高等级的聚丙烯热缩带已经在得到了应用。 由于采用低等级聚乙烯材料可能导致在工程应用中出现问题: 1、采用低密度或低等级聚乙烯材料导致在安装过程中安装工人不敢长时间的烘烤(容易烤裂),这样更加导致热缩带烘烤不透,安装后的质量不可控。 2、在太阳直射的白天,热缩带下面的气泡膨胀,安装后的热缩带表面有鼓起来的气泡。(热缩带变软后,气泡容易鼓出) 3、在70度的温度下,热缩带变软,周围的沙石等容易将热缩带顶破,管线补口防腐蚀出现严重问题。 导致采用低密度聚乙烯的原因:1、目前国标没有规定。目前国内管线的主防腐层不仅仅规定了必须采用高密度聚乙烯材料(>0.94 g/cm3),而且在实际设计的时候还要求将主管线防腐层采用加强级的设计,因为普通的高密度聚乙烯在管线运行温度条件下,还不足以抵抗周围环境的破坏,但设计补口材料时没有相关要求。2、采用高密度聚乙烯的热缩带,在生产过程中。回收料、低等级聚乙烯等无法添加,必须采用纯正的高密度聚乙烯材料。 3.5特殊的补口 在管线补口中,会存在一些特殊补口的补口。 1、热煨弯管与3层pe管之间的补口 这种部位的补口特殊性在于:热煨弯管的外防腐层为双层熔结环氧粉末结构,其材料与补口材料并不匹配。 2、短接、碰头处的补口 由于这种地方的裸露钢管宽度往往超过正常宽度,为了保证搭接宽度,往往采用两个收缩带,但是由于两个收缩带施工先后顺序不同,其质量难以保证。 3定向钻穿越段的补口、补伤 对于定向钻穿越段管道补口,应采用带配套环氧底漆的定向钻穿越补口带,其基材厚度:收缩前≥1.6mm;胶层厚度:收缩前≥1.2mm。补口系统材料由补口带、牺牲带和配套的环氧底漆构成,前面的牺牲带具有牺牲功能,保护后面正常补口带在回拖过程中的安全。定向钻穿越段热收缩套不用铁箍,在穿越过程中铁箍容易脱落,并滑伤管道防腐层。定向钻穿越段补伤片处加装牺牲带。 4、主管线补口失效的主要形式 目前管线补口失效主要表现为三种形式: a、密封失效:表现为热缩带与主管线防腐3pe涂层脱开。 b、防腐蚀涂层失效:在钢管表面的环氧底漆涂层没有形成有效的防腐蚀作用;环氧底漆与热缩带完整从钢管表面脱落。 c、热缩带主体破损严重:表现为热缩带折皱、穿透。 密封失效的主要原因:在3层聚乙烯pe涂层的防腐设计中有一条关键的要求,即:3层聚乙烯补口材料必须与主管线防腐涂层相互匹配的原则。但是目前的补口材料与主管线防腐涂层还不能很好匹配。 防腐蚀涂层失效的主要原因:环氧底漆的防腐性能不仅仅与材料本身的性能有关,更与其施工的厚度和均匀度有关,环氧底漆中有一种叫流平剂的材料,就是为了保证环氧底漆的均匀性,采用湿膜安装时其厚度和均匀性完全没有保证。除此之外环氧底漆与钢管表面的附着力缺乏技术要求。 热缩带胶黏剂的抗剪切强度,埋地管线在实际的运行过程中所受到的环境应力和土壤应力比较集中表现在对热缩带的剪切作用。根据欧洲实验室报告,在埋深1米,运行温度为50℃条件下: 管线直径 4" 16" 28" 40" 剪切强度(mpa) 0.043 0.062 0.113 0.165 而目前国内采用的技术要求中,统一将运行温度在50℃情况下的剪切强度设定为0.05mpa,由此可见目前的技术规范存在技术漏洞。 当然现场施工人员不按规范要求施工,不按规定程序施工也是导致补口失效的重要原因。 5、补口主要环节及监督 5.1、补口前准备 5.1.1材料要求 防腐材料应存放在阴凉、干燥处,严禁受潮和日光直接照射,并隔绝火源,远离热源,存放场所的温度和湿度应符合生产厂商提出的要求。热收缩带使用前应认真检查,基材边缘应平直、表面平整、清洁、无气泡和裂口及分解变色现象。防腐补口、补伤材料必须由经业主批准的生产厂商提供,并由业主检测部门出具复检报告,同时具有出厂合格证和使用说明书; 5.1.2设备要求 空气压缩机出口处应有油水过滤器,空气压缩机排气量不小于6.3m/min;液化气罐应符合安全要求,且减压阀输出压力不小于0.15mpa,数字式温湿仪、风速仪量程满足要求,且稳定显示,电火花检漏仪的输出电压应满足15kv检漏电压的要求。 红外测温仪应每天用接触式测温仪校正。 5.1.3人员要求 防腐补口补伤作业机组zui少配备8人:喷砂除锈2人,火焰加热3人,辅助施工3人;现场防腐补口、补伤操作人员必须经过防腐施工培训和考核,并取得监理或epc下发的上岗证。施工前,防腐补口带厂家专业人员和施工单位技术人员向参加防腐补口、补伤防腐操作人员进行技术交底,使每个操作人员都能熟知防腐材料的使用要求和各工序的操作要领。同时应检查管材防腐层质量,达到要求,才可以施工。此外,有时防腐补口补伤材料供应商应派技术人员对现场防腐作业进行监督和指导。 5.2、补口准备 5.2.1作业天气条件 如下情况如无有效防护措施,不应进行露天施工。 a) 雨天、雪天、风沙天。 b) 风力达到五级(8.0~10.7米/秒)以上。 c) 相对湿度大于85%。 5.2.2补口处处理 环向焊缝及其附近的毛刺、焊渣、飞溅物、焊瘤、补口处污物、油污和杂物等必须清理干净。检查管材防腐层端部是否有翘边、生锈、开裂等缺陷,如有缺陷应进行修口处理,切除到防腐层与钢管完全粘附处为止,切口边缘要作坡角处理。为防止喷砂过程中pe层损伤,管口应做适当的保护。 5.2.3其他条件 确保合适的作业空间,粤桂项目部规定管底对地净距小于500mm时不得施工,如作业空间不足,需进行土方开挖,以保证足够的空间。管口清理前应记录补口处未防腐的宽度。 5.3、喷砂除锈 5.3.1预热 喷砂除锈使用的石英砂粒径应在2-4mm之间,必须干燥,无油、无污染,严禁使用粉砂。石英砂应存放在清洁干燥处。喷砂前要监测露点,对管口表面加热:将管口预热至40-50℃(冬季,适当提高预热温度至70-80℃) ,确保钢管预热温度高于露点3 ℃以上。粤桂地区空气潮湿,预热时间要延长,保证管口潮气驱除干净,避免二次返锈。管口加热完毕,应采用接触式测温仪或经接触式测温仪对比校准的红外线测温仪测温,测量管口周向均匀分布至少4个点温度,各点温差不大于±5℃,方可进行喷砂除锈。 5.3.2喷砂 喷砂应在补口下风方向进行,喷砂工作压力宜为0.4-0.6mpa。喷砂应连续进行,喷枪与管道表面应保持垂直,以匀速沿管轴线往复移动,从管顶到管底逐步进行。管口表面处理质量应达到sa2.5级,锚纹深度35-70微米,清除表面灰尘。 5.3.3打毛 喷砂除锈完成后应及时进行防腐补口。将环向焊缝两侧防腐层与补口材料搭接范围内的pe层表面作打毛处理。打毛宽度应与热收缩带覆盖宽度基本一致。 将热收缩带与管体涂层搭接处清理干净并加热,用钢丝刷将其打毛,完毕后,应清除浮渣;pe层打毛深度及密度约为1mm,沿竖向及斜向打毛,所有打毛区域都必须打毛到位,特别要注重检查12点位和6点位的打毛质量。对pe层需打毛的区域,建议分段适度加热,打毛时,pe层的加热温度不宜过高,更不得将pe层烤流化。 a. 钢管、搭接部位的预热:将补口部位的钢管和搭接部位的pe层均匀预热到40℃-60℃,建议环境温度较高时,宜在40℃-50℃范围内选择;天气转凉,宜在50℃-60℃范围内选择;b. 底漆的涂刷:将搅拌好的底漆迅速均匀涂敷在补口处的钢管表面及搭接处的pe层上,被打毛区一定要涂刷底漆,涂刷宽度与热收缩带覆盖宽度基本一致。 基料(a 组份)需加热才能搅拌均匀时,待其温度降至 40℃以下,再将固化剂(b 组份)全部加入并搅拌均匀,如果温度高引起提前固化,会影响底漆流动性和粘性。 5.4、热收缩带施工 5.4.1热收缩带的具体施工见附件。 5.4.2热收缩带施工的主要步骤其原理如下: 1、喷砂除锈 喷砂除锈一般采用抛丸除锈它不仅能够彻底清除钢管表面的铁锈和氧化皮,配合砂粒大小还能得到理想的钢管表面粗糙度(锚纹深度)。清洁的砂粒和干燥无油的压缩空气有助于得到理想的喷砂效果。喷砂除锈这道工序非常重要,它能保证涂覆的底漆对钢管具有良好的附着力,直接关系到防腐质量的好坏。 2、喷砂前钢管预热 钢管补口部位必须预热至高于露点3℃以上,否则,表面处理质量会受到影响,而且除锈后的钢管表面在加热安装热缩带时,容易出现浮锈,必须再次喷砂除锈,否则会影响涂装质量。 3、配制底漆 环氧底漆的b组分必须全部倒入a组分罐中并充分搅拌均匀,确保底漆达到理想的交联密度。致密的漆膜是判断防腐层隔离腐蚀介质性能的重要依据之一。比例不准确混合不均匀的底漆将影响热熔胶与底漆的粘接。 4、防腐层打毛 对接头两侧将要包覆的防腐层用钢丝刷沿周向打毛的目的是增加防腐层的表面粗糙度,增大其表面积,利于分子吸引和机械锚固作用,底漆和防腐层的附着力会增加。即便于浸润,促进粘结。 5、刷底漆前预热钢管 增加pe极性,实现与环氧的粘结。对钢管的预热是为了保证热缩带接触到钢管时,不至于因钢管表面温度过低使热熔胶表面快速硬化,失去充分的流动性和浸润性,达不到良好的粘结效果;对防腐层的预热既为了使其具有一定的温度,便于底漆的流动和浸入,另一方面,预热使聚乙烯防腐层具有一定的极性,这两个因素都会增强底漆与防腐层的粘结力。 6、底漆涂刷(湿膜) 环氧固化过程中与钢管表面及热熔胶中的活性基团均形成牢固的稳定的化学键,其键能远高于色散力、偶极力等其他类型的分子间力,达到有效的、持久的粘结。正是由于热熔胶和底漆的粘接是化学反应型粘接,所以任何不利于热熔胶和底漆产生化学反应的因素都应该避免,比如:钢管和防腐层的温度不能预热太高,太高会让底漆提前固化,使其与热熔胶反应的活性基团大大减少;底漆涂刷后不能再对底漆进行烘烤也是同样的道理。 7、胶条的利用(部分产品) 在热缩带端部的钢管上沿轴向粘贴胶条的目的是降低因热收缩带厚度所带来的高低落差,减少气泡的产生。 8、回火 热收缩带整体收缩完成以后,热熔胶并没有完全熔化。前面提到热熔胶要和环氧底漆产生化学反应,这种反应需要温度和时间。所以整体收缩完成后,应对热缩带整体再加热,使其表面温度始终保持在150℃~180℃不少于3分钟,这个过程至关重要,它除了能让热熔胶熔化成流体与底漆充分接触,还为两者的化学反应提供了充足的时间和热量。 9、注意事项 (1)喷砂除锈后的钢管用红外线测温仪测量温度会偏低,如涂刷底漆时,出现冒烟、快速固化等现象,说明温度过高,应停止补口操作,用接触式测温仪校准后,再用红外线测温仪进行测量。 (2)若环境温度低于-5℃,请在施工前对热缩带进行保温处理。 (3)热缩带整体收缩完成后的再加热,应确保温度始终保持在150℃~180℃不少于3分钟。当天气转凉后,应根据环境温度,管径大小,将保持时间延长至5~8分钟。 (4)安装收缩前,不能将热缩带从小包装中取出以免被砂石划伤或沾灰。 (5)安装烧缩过程中用火应均匀,避免局部碳化。 (6)为了均匀收缩,减少气泡,在热收缩带两端垫上3对木衬,使上下左右预留量大体一致。采用3人用中火从中央沿环向两侧均匀移动加热,从管顶到管底逐步使热收缩带均匀收缩。在加热过程中,三人应处在相对应的位置,同步同一方向进行,避免产生气泡和皱褶。热收缩带两端垫上3对木衬,三人处在相对应的位置,同步同一方向烤缩。如果气温低应增至4个烤把。 (7)防止翘边:当加热收缩至坡口处时,取出木衬。继续加热热收缩带,直至端部收缩紧密。当热收缩带收缩到边缘时,火焰应覆盖热收缩带的边缘多加热数秒(火焰中心对准边口,一半覆盖热收缩带一半覆盖pe层),使之收缩紧密,防止收火后产生翘边。在加热边缘时,避免火焰加热到热收缩带的内侧而导致底漆失粘。 5.4、热收缩带常见问题 5.4.1导致热收缩带出现质量问题的主要原因: (1)技术标准和技术规范不符合实际要求; (2)补口材料自身质量问题; 即便合格的补口材料其长期抗腐蚀性能不一定能满足管线运行的要求,此外实验室检测结果和实际应用的结果相差很大。 (3)现场施工工艺不合理; (4)现场监督不严。 5.4.2常用的检测方法 (1)资料检查、人员资格检查 包括补口材料出厂合格证及质量检验报告;补口施工记录及检验报告,同时对施工人员的资格进行检查,防止违规施工。 (2)外观检查 直观检查热收缩带表面平整光滑程度,看其是否有皱褶、翘边及烧焦碳化现象;检查与三层pe搭接处热收缩带的溢胶是否充分、均匀、连续。 (3)试验检测 工程上常用对热收缩带检测方法包括:电火花检漏和局部剥离检测,但是这两种方法都不能反映整个补口的真实情况;实际检查中可以靠手指弹击热收缩带以确定其下方是否存在气泡,尤其是补口六点位钢管与pe层交界边缘容易出现气泡。 (4)监督不力 施工完毕后各有关方应进行严格的检查,对出现问题的补口带及时发现、及时整改。 5.4.3常见问题及解决方法 1.热收缩带翘边 可能原因: a.烘烤不到位,导致热收缩带边缘未真正收缩到管体上并形成良好粘结。 b.底漆在钢管主体防腐上的涂刷宽度不够,甚至没有将底漆涂刷在主体防腐上。 解决办法: a.对热收缩带边缘烘烤直到其完全收缩到位并充分回火,确保粘结良好。 b.在防腐层上底漆涂刷尽量薄,防腐层涂刷宽度应超出热缩带实际搭接宽度3cm~5cm。 2.上面轴向宽度小,底部轴向宽度大 可能原因: 底部余量太大,导致其自由收缩而涨长。 解决办法: 安装热收缩带时,在钢管顶部或2点10点位垫上木撑,尽量减少热收缩带底部的余量。 3.热收缩带与底漆钢粘接不牢 可能原因: a.预热温度太高,导致底漆刷上后迅速固化,影响环氧与热熔胶反应,导致粘接不牢。 b.底漆涂刷后没有及时安装热收缩带,底漆已经部分固化影响粘接。 c.回火时间及力度不充分,因西二线产品是高温型热收缩带,再加上是大口径钢管补口,如果回火不充分会导致粘接不牢。 d.底漆混合不均匀。 e. 钢管上局部没有涂刷底漆。 解决办法: a.预热温度严格按照产品说明书的要求,用红外点温计测量50-60℃。 b.底漆涂刷后在3分钟以内必须安装热收缩带。 c.热收缩带整体收缩完毕后,回火时间及力度应充分,使表面温度保持在150℃~180℃不少于3分钟(冬季不少于6分钟),现阶段宜在此基础上再延长2分钟。 d.将底漆的b组分全部倒入a组分罐中后,充分搅拌,直到两个组分混和均匀。 e.钢管整体都涂刷底漆,防止漏涂。 4.热收缩带与管道防腐层(pe)粘接不牢 可能原因: a.与热收缩带与底漆钢粘接不牢的五条原因相同。 b.对管道防腐层进行打毛以后没有再对其进行预热。 解决办法: a.与热收缩带与底漆钢粘接不牢的办法相同,严格控制防腐层预热温度70-80℃,并将热缩带需包覆的主体防腐层都涂上底漆。 b.防腐层刷底漆前一定要确保防腐层已经预热。 c.当热收缩带收缩到防腐层坡口处时,可以向热收缩带的胶面灌火操作。 5.固定片翘边 可能原因: 用火不够,造成粘接不良而翘边。 解决办法: a.安装固定片时,要对固定片的胶面加热直到其热熔胶完全软化。 b.热收缩带安装完毕以后在固定片的两端宽度方向各安装一根胶条进行封边,将环氧罐内剩余的底漆涂刷于固定片的另外两边。 6、站场内防腐补口 站内管道防腐、焊接安装后需要对焊接部位进行喷(抛)射除锈与补口。表面处理应达到 gb 8923 规定的 sa2.5 级,焊缝应处理至无焊瘤、无棱角、无毛刺。站内三层 pe管道补口采用热收带补口(带配套底漆),其它防腐层的埋地管道补口都采用液态环氧与聚丙烯增强编织纤维防腐胶带方式。聚丙烯增强编织纤维防腐胶带的施工应在无溶剂环氧防腐层检查合格后进行,并应除去无溶剂环氧防腐层表面的灰尘和湿气。采用螺旋缠绕方式施工,螺旋缠绕搭接宽度 55%,一次完成双层胶带的施工。 注:sa1 轻度的喷射或抛射除锈:钢材表面应无可见的油脂和污垢,并且没有附着不牢的氧化皮、铁锈和油漆涂层等附着物。sa2 彻底的喷射或抛射除锈:钢材表面应无可见的油脂和污垢,并且氧化皮、铁锈和油漆涂层等附着物已基本清除,其残留物应是牢固附着的。sa2.5 非常彻底的喷射或抛射除锈:钢材表面应无可见的油脂、污垢、氧化皮、铁锈和油漆涂层等附着物,任何残留的痕迹应仅是点状或条纹状的轻微色斑。sa3 使钢材表观洁净的喷射或抛射除锈:钢材表面应无可见的油脂、污垢、氧化皮、铁锈和油漆涂层等附着物,该表面应显示均匀的金属色泽。 7、补伤 7.1管道防腐层、补口处补伤 补伤片的性能要符合要求:1、对深度小于防腐层厚50%的损伤,用热熔修补棒/补伤胶补伤。2、直径不大于30mm且深度大于防腐层厚50%的损伤(包括针孔),采用补伤片补伤。3、直径大于30mm且深度大于防腐层厚50%的损伤,先用补伤片进行补伤,然后用热收缩带包覆。 7.2补伤方法 准备好使用的工具和补伤材料,密封胶和补伤片与管体防腐材料相容,由同一生产厂商提供。1、直径不大于30mm损伤的修补:先铲除已破损的防腐层,再用小刀把边缘修齐,边缘坡角小于30°,损伤区域的污物应清理干净,并把搭接宽度100mm范围内的防腐层打毛,用火焰加热器预热破损体表面,温度宜为60℃-100℃,在破损处填充尺寸略小于破损面的密封胶,用火焰加热器加热密封胶至熔化,用刮刀将熔化的密封胶刮平。剪一块补伤片,尺寸应保证其边缘距防腐层孔洞边缘不小于100mm,补伤片剪去四角形成圆滑曲线,将补伤片内层烤软、发粘,迅速将补伤片的中心对准破损面贴上,用火焰加热器加热补伤片,用压辊抚平、滚压,边缘有胶溢出,补伤完成。(控制辊压力度防止胶粘剂过多溢出。)2、直径大于30mm的损伤,伤口处理和不大于30mm的方法相同,再用热收缩带包覆。(加热热收缩带时要符合要求。) 7.3补伤主要环节 补伤的主要环节: a)用刀修理pe防腐层上的破损处,防止破损处扩大。 b)用清洁溶剂清除暴露在外的钢表面和邻近防腐层上的油脂和污物。 c)用砂纸或钢丝刷除管线上的铁锈及防腐层上的粉末、污物。打磨需修补的区域。 d)将混合好的环氧底漆涂敷在所有裸露的金属表面。 修补棒: a)用低强度的黄色火焰预热需修补处及其周边,预热需修补的地方除去潮气、湿气。 b)用火把加热修补棒直到其软化流动。 c)把修补棒放在破损处,用火把同时加热修补棒和修补处,火把保持移动防止防腐层的破损。 d)继续涂抹修补棒直到完全覆盖破损处。 较深的伤口采用填充料: a)用低强度的黄色火焰预热需修补处及其周边,预热需修补的地方除去潮气、湿气。 b)将填充料放在需修补处,揭去填充料上面的保护膜,紧紧地按压材料使其贴紧需修补处。 c)填充材料放在修补处后,去除表面不平整的材料,用低强度的火焰加热材料。 补伤片的使用: a)预热破损处,预热区域为破损处及搭接处。 b)去除补伤片的保护衬垫,带上手套将补伤片带粘性的向上或放在管线上,慢慢加热直至胶粘剂变软,表面出现光泽。加热破损处使它具有一定的表面温度。 c)将胶粘剂变软的一面放在破损处,向下按压,用低强度的火焰加热补伤片,用辊轮压平补伤处,确保补伤片完全粘接。补伤片补好后四周应有有规则溢胶。 7.4补伤质量检查验收 1、补伤后的外观应100%目测,表面平整,无折皱,无气泡及烧焦碳化现象,不合格应重新补伤。2、补伤处应100%电火花检漏,检漏电压15kv,无漏点为合格。3、补伤的粘结力按要求抽查,管体温度为10℃~35℃时的剥离强度不低于50n/cm,每50个补伤抽查一个,如不合格,加倍抽查,若加倍抽查不合格,则该段管线的补伤应全部返修。 热煨弯管的补伤:直径小于或等于25mm的伤口,应用环氧粉末供应商推荐的热熔修补棒或双组分液体环氧树脂涂料进行局部补伤,直径大于25mm,且面积小于(2×104)mm2的伤口,应用环氧粉末供应商推荐的双组分液体环氧树脂涂料进行局部补伤。补伤后防腐层厚度大于等于800μm。与本文相关的论文有:矿山电动插板阀 |